Кованый или прокатный и другие заблуждения. Часть 1
Пролог
В основе всех рассуждений на тему какой нож лучше — из кованой стали или из прокатной, лежит прочный стереотип, что при ковке сталь улучшается, а при прокатке, должно быть, портится или как минимум не улучшается. Иногда еще можно услышать фразы «штампованная сталь» или «штампованный нож», которым придается крайне негативный оттенок и воспринимается, как что-то заведомо некачественное, худшее, нежели столь благородно звучащее — «кованый нож».
Необходимо внести ясность, что на самом деле штампованная сталь сама по себе не существует отдельно от того или иного конкретного изделия, получаемого методом штамповки, а ножи как раз методом штамповки не производят вообще. Штамповка это процесс формовки материалов посредством давления штампом определенной формы. Но к клинкам ножей это не относится, потому что технологически нет нужды — нечего там штамповать. Про ширпотребные китайские кухонники мы тактично не упоминаем, так как большинство из них всё-таки очень трудно называть полноценными ножами.
Если обобщить, именно клинок ножа, с его характерной формой и габаритами, может быть получен двумя способами:
1. Объемная горячая формовка из заготовки стали почти любой формы, то есть методом ковки, причем преимущественно ручной — молотком на наковальне. Это подразумевает случаи единичного производства клинков, когда над каждым из них работает кузнец с молотком и вручную формует клинок требуемого размера и конфигурации.
2. Резка. Начиная от человека с ножовкой по металлу, заканчивая лазерным станком с программным управлением. Осуществляется методом вырезания из заготовки заведомо плоской формы, которая в свою очередь может быть получена либо прокаткой, либо ковкой. Причем самое интересное, что на сегодняшний день практически любая кованая заготовка для будущего клинка производится методом ковки из стального прутка, который в свою очередь был получен опять же методом проката.
Так что такое кованая сталь
и чем она отличается от не кованой, если всё равно изначально получается из прокатной?Ясно, что нас интересует не просто технологическая разница, но различие результативное, по факту, чем так называемый «кованый нож» лучше ножа из прокатной стали? Ведь не даром можно слышать от многих производителей, что их ножи кованные, а потому заведомо лучшие. Без каких-либо объяснений и доказательств. И подавляющее большинство потенциальных покупателей замечательно подкупается подобными лозунгами, кстати так же, как и словом «булат». Производители это прекрасно осознают и пользуются ситуацией, а именно, отсутствием у покупателя понимания процессов, происходящих со сталью во время производства.
Чтобы разобраться во всей этой путанице, важно обозначить главный момент: решающим является вопрос терминологии. Не определившись с терминами, трудно что-либо согласовать и уложить по полкам. Жонглируя словами «простой, булатный, порошковый, кованый, прокатный» и их сочетаниями можно вводить человека в заблуждение бесконечно долго. Это фразы, которыми оперируют коммерчески продвинутые производители, сути происхождения стали они не отображают, и о свойствах каждого конкретного ножа они ничего не говорят.
Поэтому необходимо чётко разделить понятия: что такое нож кованый и нож не кованый.
Глава 1. Ковка, как необходимость
Кованый нож, а точнее говоря, кованый клинок — это когда из заготовки стали, неважно какой формы, человеком вручную формуется контур и геометрия клинка, вытягивается хвостовик, оттягиваются будущие спуски.
Применяется такой метод только в условиях единичного производства ножей одним мастером или немногочисленной группой мастеров. С точки зрения целесообразности метод обоснован в случаях:
1. Если изначальная заготовка стали не совсем подходящей формы. Например, из круглого подшипника одним только способом резки клинок не получить.
2. Ковка клинка в чистовой размер как способ экономии материала. Это объединяет как древних кузнецов, которые знали истинную цену сырью для производства оружия и инструмента, так и современных мастеров, бережливо кующих клинки из полосы дорого купленной стали, просто потому что отрезать лишнее и выбрасывать — расточительно.
3. Когда усиленная деформация осуществляется с целью повлиять на некоторые составляющие структуры стали. В частности, если стоит задача несколько раздробить плотные скопления карбидов в сталях с их высоким содержанием и неравномерным распределением.
Кстати, такой подход дробления твердых фаз принципиально характерен вообще для производства сталей с изначально высоким содержанием крупных карбидов и их скоплений — быстрорежущих, некоторых штамповых сталей (не путать слова «штамповый» и «штампованный»)
После непосредственного производства, то есть выплавки, в своем самом первичном виде эти стали содержат настолько крупные скопления карбидов, что их подвергают прокатке и ковке, то есть сильной горячей деформации, до тех пор, пока карбиды не измельчатся до определенного размера. Явление называется карбидной неоднородностью и имеет несколько чётко обозначенных степеней.
В противном случае, к примеру, быстрорежущая сталь с недостаточно раздробленными включениями карбидов считается бракованной. Поскольку крупные карбидные включения являются очень твердыми и хрупкими, то зуб пилы, фрезы, или сверло, на режущую кромку которого попадает такой нежелательный фрагмент, обречено на неизбежное выкрашивание.
Если проводить аналогию с ножом, режущая кромка которого геометрически отличается от режущей кромки фрезы, как яхта от ледокола, то для тонкой и острой РК ножа наличие огромных, твёрдых и хрупких элементов в структуре сказывается еще более плачевно.
Это к слову о так называемых «булатах», как исторических, так и новодельных, у которых степень карбидной неоднородности настолько высока, что густые скопления карбидов в виде различных узоров можно без труда разглядеть невооруженным глазом на расстоянии вытянутой руки.
И это в противовес не имеющим никакого узора современным порошковым быстрорежущим сталям, в составе которых содержание сверхтвёрдых карбидов тугоплавких металлов очень велико, но они имеют минимально возможный размер и максимальное распределение, что позволяет таким сталям демонстрировать колоссальные результаты по удержанию остроты режущей кромки.
Глава 2. Реалии ножевого производства
Ручная ковка стали, в комплексе с другими циклами термообработки, нацеленными на создание необходимой структуры — это метод, позволяющий получить качество ножа, отличное от качеств, свойственных подавляющему большинству других ножей из той же самой стали, но производимых на потоке, к которым применяются стандартные режимы ТО.
Для неискушенных пользователей, разница в стоимости между такими ножами зачастую перекрывает разницу в реальных преимуществах. Поэтому в условиях множественного производства ножей ручная ковка клинков и применение специальных режимов термообработки являются необоснованными с точки зрения экономики предприятия, выпускающего ножи в большом количестве.
Все так называемые «кованые ножи» в условиях современного поточного производства — это когда из прокатного прутка методом ковки на пневмомолоте получают поковку-полосу, из которой потом болгаркой вырезают клинки. После чего, как правило, сразу следует закалка, то есть о какой-либо предварительной термообработке, нацеленной на подготовку структуры к закалке, устранение структурных напряжений после ковки, а так же уменьшение зерна металла, речи не идёт.
Соответственно, совсем не факт, что эти клинки будут лучше, чем так же вырезанные из полос, прокатанных и отожженных сразу на металлургическом заводе, минуя стадию расковки на пневмомолоте из кругляка кузнецом, квалификация которого всегда остается загадкой для покупателя. И хотя в каталогах многих отечественных производителей сегодня можно встретить модели ножей со следами, дескать, «ручной ковки», не обольщайтесь — от того что по заранее вырезанной пластине для рельефа немножко постучали молотком за пару бестолковых нагревов, сталь лучше, увы, не становится.
И тут назревает самый важный вопрос: тогда от чего же всё-таки сталь становится лучше?
Ответ простой: сталь становится лучше от применения осознанной целевой и качественной термообработки. И нужно понимать, что качественная термообработка это не просто хорошая закалка клинка, но весь комплекс мероприятий, связанных с температурным воздействием на сталь, в том числе это относится и к горячей деформации стали.
Причём без громадной принципиальной разницы, происходила ли она под воздействием динамической нагрузки, то есть с ударами молота, либо под более плавным воздействием — при прокате в стане. Поэтому попытка производителя на словах выдать якобы «кованый» нож в качестве заведомо лучшего, нежели прокатный, должна подвергаться здравому скептицизму и вызывать встречные вопросы с просьбой описать технологическую последовательность производства этих хвалёных кованых ножей.
Однако, в жизни между двумя методами горячей деформации, ковкой и прокатом, разница всё же есть. И очень часто она серьёзно сказывается на качестве обрабатываемой стали, а значит и на качестве конечного изделия.
Продолжение следует….
Автор: URAL MADE.COM
knife-mag.ru
Способ выбора / Том 1 / Глава 864: Носильщик, выкованный из стали
Глава 864: Носильщик, выкованный из стали
Вниз по течению появилось около десяти боевых кораблей, принадлежащих Флоту Великой Чжоу, на каждом из которых было много солдат, снаряженных божественными арбалетами.
Многие эксперты Имперского Двора со свистом отправились на берег и побежали в Город Фэнъян.
Несколько даосистов, чья синяя одежда развевалась вокруг них, вылетело из леса на противоположный берег. Они мягко коснулись кораблей и приземлились на другой берег.
У даосистов в синем одеянии, орудовавших мечами дао, были холодные, непостижимые выражения лиц. Они прибыли из Монастыря Вечной Весны в Лояне.
Разорванная кожаная обувь, ступающая на каменные ступеньки, все еще не высохла от утренней росы.
Чайные торговцы и пешеходы на обеих сторонах каменных ступенек подсознательно отступили с приближением этого человека, возможно, из-за страха или из-за стыда.
Сяо Чжан даже не смотрел на этих людей, игнорируя экспертов Имперского Двора, преследующих его. Держа копье, он невыразительно продолжал двигаться вперед.
Из какого-то угла улицы послышалось несколько вздохов, которые затем стремительно исчезли. Среди беспокойной толпы был смутно виден холодный блеск арбалетных болтов.
Облаченные в синее даосисты взлетели на каменные ступеньки, как журавли. Они были за Сяо Чжаном с мрачными выражениями лиц, готовясь напасть в любой миг.
Путь от реки до Крепости Семи Сокровищ был полностью сделан из каменных ступенек. Кто-то, кому было нечего делать, однажды посчитал их, узнав, что тут было более семи тысяч ступенек.
Обычному человеку потребуется очень долгое время, чтобы пройти их все.
Но Сяо Чжану, даже пострадавшему от тяжелых ранений, не потребовалось много времени.
Он через несколько мгновений достиг середины лестницы. В стороне был очень маленький парк.
Несколько десятков людей стояло в этом парке в тени деревьев, наблюдая за ним с довольно сложными выражениями лиц. Они немного боялись, немного беспокоились.
Вдруг невероятно тусклый и скрытный проблеск меча пронзил корзину, которую держал один из этих людей, устремляясь к Сяо Чжану.
Это был непостижимый угол атаки, наиболее коварный удар.
Но похоже, что Сяо Чжан был давно готов к этому. Он заворчал, пронзая копьем воздух, с точностью поражая проблеск меча со свирепым импульсом.
Проблеск меча раскололся на части, и ассасин, скрытый в толпе, был вынужден отступить в ужасном состоянии, ударяясь о дерево.
Листья полетели на тело ассасина, быстро окрашиваясь в красный цвет кровью.
Лицо ассасина наполнилось испугом. Он хотел встать и убежать, но уже не мог собрать силы.
Сяо Чжан на удивление только взглянул на ассасина прежде, чем продолжить идти по ступенькам.
Группа Чэнь Чаншэна уже покинула чайный дом и сейчас стояла за толпой.
Видя эту сцену, Танг Тридцать Шесть похвалил: «Превосходная техника».
Во время ночи переворота Мавзолея Книг и в последующий период Сяо Чжан был неподатливым врагом для Ортодоксии, но все изменилось после того, как он спас Ван По на берегах Реки Ло. По крайней мере, по мнению Танга Тридцать Шесть этот эксперт, который должен был быть на вершине Провозглашения Освобождения, был могущественным союзником, за которого они должны были бороться, так что у него был благоприятный взгляд на него.
Но Ху Тридцать Два и Чжэсю покачали головами, услышав похвалу Танга Тридцать Шесть. Было очевидно, что у них были отличные взгляды.
«У него слишком серьезные ранения. Даже более серьезные, чем мы представляли», — с волнением сказал Чэнь Чаншэн.
Танг Тридцать Шесть понимал.
Судя по дикому стилю сражения Сяо Чжана, если бы у него все еще было шестьдесят или семьдесят процентов его боевых возможностей, даже ассасин из Павильона Небесных Тайн погиб бы от одной атаки, а его кости потрескались бы.
Даже если бы он смог выжить каким-то чудом, характер Сяо Чжана гарантировал, что последовал бы другой удар, убеждаясь в его смерти.
Но ассасин все еще был жив.
Это только могло означать, что раны Сяо Чжана были более серьезными, чем они представляли, настолько серьезными, что он даже не желал тратить энергию на еще один удар копья.
Как и ожидалось.
Несколько экспертов Имперского Двора использовали беспокойство толпы для атаки Сяо Чжана.
Сяо Чжан успешно отбился от этих экспертов, но его тело начинало покачиваться, готовясь упасть в любой момент.
«У него новые раны, и даже больше старых ран».
Как и Сяо Чжан, Чжэсю относился к битве, как к способу жизни. Его глаза запросто определили проблемы с Сяо Чжаном.
После того, как его преследовал Имперский Двор три года, бесконечно сражаясь без мгновения для отдыха, даже если тело Сяо Чжана действительно было выковано из стали, он все еще почувствовал бы себя уставшим.
Как только он станет уставшим, его скорость реакции замедлится, из-за чего ему будет проще получить раны.
Как только он начнет получать раны, он продолжит получать все больше и больше ран. Его истинная эссенция высохнет. Он станет невыносимо измотанным, и наконец-то лишится сил давать отпор.
Он был пиковым экспертом Конденсации Звезд Провозглашения Освобождения, и для него было редко найти кого-то не в Божественности, кто мог сравниться с ним. Он был подобен какому-то гигантскому зверю, в одиночестве странствующему по пустошам. Он не имел возможности контратаковать, и его так много дней преследовали те стервятники, которыми были эксперты Имперского Двора, вынуждая сражаться в течение его долгого путешествия. Рано или поздно наступит день, когда его тело рухнет на землю.
Сяо Чжан наконец-то достиг самой высокой точки Города Фэнъян.
Он стоял перед Крепостью Семи Сокровищ. Сяо Чжан прищурил глаза, глядя на реку внизу.
Над горами уже взошло утреннее солнце. Его пылающие лучи сияли над рекой и горами, их сияние было довольно ослепительным.
Он мог ясно видеть, что эксперты Имперского Двора и божественные арбалетчики уже окружили Город Фэнъян.
Хотя его разум все еще был в порядке, он был раздражен, как будто увидел стаю мух, которых не мог разогнать.
Такой человек, как Сяо Чжан, действительно мог считать себя гигантским зверем, в одиночестве бродящим по пустошам, но он никогда не признает, что эти эксперты Имперского Двора, преследовавшие его несколько лет, были стервятниками. В его глазах они были раздражительными мухами и комарами, каждый день жужжащими возле его ушей, из-за чего ему было трудно заснуть, и именно поэтому сейчас он чувствовал себя настолько сонным.
Да, он просто был немного сонным.
Он чувствовал, как будто ему требовалось немного поспать, иначе почему бы его веки были такими тяжелыми, губы — такими немыми, а его преследователи догнали его?
Он чувствовал себя все более сонным и сонным, а его веки были все тяжелее и тяжелее. Даже он найдет трудным различить, щурились ли его глаза или уже были закрыты.
Утреннее солнце засияло на Город Фэнъян и на его лицо.
Он покачнулся дважды, а затем упал на пол.
Но он не скатился по ступенькам.
Конец его копья с глухим ударом ударился о землю. В самый опасный момент оно помогло поддержать его уставшее тело.
При этом зрелище многие люди, которые никогда не забывали все добро, сделанное Сяо Чжаном для Города Фэнъян, больше не могли смотреть, и отвернулись. Но некоторые люди встали.
Первым, кто встал, был чайный торговец Города Фэнъян, а также около десяти помощников магазина, работавших в чайном бизнесе.
«Защитите Господина Сяо!»
Чайный торговец сжал зубы и закричал, а затем взял с собой этих помощников магазина вверх по каменным ступенькам к Крепости Семи Сокровищ и встал перед Сяо Чжаном. Некоторые из них вынули мечи, которые они обычно держали при себе для защиты, но еще больше использовали шесты, обычно предназначающиеся для переноса товаров, указывая ими на приближающихся экспертов.
Как чайный торговец, он неизбежно столкнется с проблемами, занимаясь бизнесом, и неизбежно вступит в конфликт с другими чайными торговцами Города Фэнъян. Этот чайный торговец был известен за свой яростный нрав, а помощники под ним тоже были невероятно доблестными, обладая некоторой репутацией в городе, иначе как бы они одни смогли остановить этих экспертов и божественных арбалетчиков Имперского Двора?
Но вскоре к ним присоединилось еще больше торговцев чаем и обычных людей.
Каменные ступеньки Крепости Семи Сокровищ были быстро переполнены людьми.
ranobehub.org
Ковка ножа — из чего лучше и проще начать изготовление
Кузнечное дело довольно непростое в освоении, слишком многими знаниями нужно обладать в области материаловедения и металлообработки. Однако, любому ремеслу можно научиться.
Ковка ножа — это одна из технологий, которую можно изучить без особых затрат. Что нужно знать о таком виде работ. Какими материалами и приемами нужно воспользоваться, чтобы получить качественное изделие?
С чего начать ковку ножей
Как и любое изделие, ковку ножа нужно начинать, во-первых, с выбора модели, во-вторых, чертежа, и, в третьих, подбора нужного материала.
Выбор модели и чертеж
Для новичка в кузнечном деле лучше всего практиковаться в поковке самых простых типов ножей. Не стоит сразу планировать изготовить какое-то супер приспособление для выживания сложнейшей формы, с долами, серейторами и прочими атрибутами.
Самым простым в изготовлении будет кованый тип клинка — финский. Он не имеет сложных форм и прочих излишеств, которые вызовут затруднения в изготовлении у начинающего кузнеца.
Простой чертеж финского ножа

Три типоразмера якутских ножей
Второй тип ножа, который можно попробовать изготовить — якутский. На сегодня в сети очень много информации по изготовлению таких клинков. Сложность его ковки в том, что он имеет выпуклую часть с одной стороны и вогнутую (дол) с другой. Однако, особенность этого ножа в том, что традиционно он не имел закалки для его простой заточки о любой подходящий камень. По размерам изготавливают три вида якутского клинка.
Набросав чертеж-схему будущего изделия, приступают к подбору нужного материала.
Материал
Сталь для ковки ножей должна обладать несколькими основными свойствами.
- Твердость и пластичность.
- Устойчивость к коррозии.
- Свойства закалки.
Лучшим выбором для изготовления клинка станут марки инструментальной легированной стали, например: Р6М5 (идет на изготовление полотен для ножовок, сверл, резцов), 9ХС (напильники), ШХ15 (подшипники) и другие образцы.
Как понять в домашних условиях, какой сорт стали есть у Вас? Обычно большинство изделий по ГОСТу имеют маркировки, на которых указывают марку материала или его состав.
Стоит учитывать, что в процессе ковки часть металла будет утеряна (уйдет как окалина), поэтому нужно брать заготовку с объемом, превышающим конечные параметры клинка. Самый простой способ получить достаточное количество материала для ковки ножа — взять напильник или подшипник.
Подобрав нужный вид материала, приступают к его обработке и формированию изделия. Как осуществляется ковка ножа из напильника?
Как ковать клинок из напильника
Для ковки потребуется стандартный набор кузнеца: горн, наковальня, пара молотов (один 1,5-2 кг, и 0,3-0,5 кг), клещи, щетка по металлу.
Подготовка материала
Изготавливая нож из напильника кузнечным способом, первое, что потребуется, это обжечь сталь. Процедуру делают следующим образом.
- Разжигают огонь в печи (не газовой!) и закладывают заготовку в очаг.
- Выдержать металл в огне примерно 4-5 часов.
- Дать остыть заготовке вместе с печью.
Это делается с целью отпустить металл, так как в инструментах он дополнительно закален и, если этого не сделать, при ковке возникнут напряжения в структуре.
Температура обжига должна составлять 600-700 градусов. Проверяют ее, посыпая заготовку солью: если она плавиться,значит, процесс идет правильно. Важно, чтобы металл раскалился равномерно по всей длине (одинаковый равномерный цвет).
После обжига температуру горения нужно уменьшать постепенно, после чего оставить заготовку в тлеющих углях до полного остывания (по времени около суток). Если остудить разогретый металл очень резко, то он попросту может растрескаться или даже раскрошиться.
Ковка
При соблюдении всех технологий ковки ножа в домашних условиях, процесс будет несложным и уже с первой попытки может получиться довольно неплохое изделие. Ковку простого прямого клинка делают по следующему алгоритму.
- Заготовку из напильника нужно поместить в горн и довести до требуемой ковочной температуры. Например, для марки стали 9ХС, она составляет верхний предел в 1180 градусов, нижний — 800.
Проверяем по цвету раскаленной заготовки, используя шкалу температур и окраски стали.
- Когда нагрев достигнет требуемого предела, заготовку клещами укладывают на наковальню и проковывают ее (обжимают). Всю поверхность нужно обжать за один нагрев.
Формовка полосы
- После металл разогревают и начинают формировать полосу приблизительно требуемой толщины.
- Спуски клинка можно будет сформировать после окончания ковки — на наждаке или применив болгарку. Однако, можно это сделать и ковкой, придав ножу нужное сечение в поперечнике.
- Заготовку опять нагревают и проковывают место, где будет рукоять — хвостовик. При этом нужно отступить немного меньше длины края полосы, примерно две трети от планируемой рукояти. При формовке хвостовика он вытянется и примет нужную протяженность.
Ковка хвостовика
- Также, вместе с хвостовиком, поковкой придают конфигурацию плечам клинка (место, где сходятся хвостовик и лезвие).
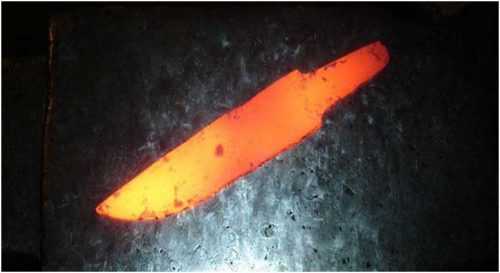
Пример сформированного клинка
- По окончанию выкованный нож оставляют в горне до полного остывания.
Немного другая технология будет при изготовлении якутского ножа. Клинок нужно формировать полукруглого сечения, а после формируют дол с противоположной стороны.
Алгоритмы поковки якутского ножа можно посмотреть в представленном видеоматериале:
Ковка ножа из подшипника более сложный технологический процесс для начинающего кузнеца. Но все будет зависеть от планируемых размеров клинка. Например, можно сделать неплохой нож при ковке из единственного ролика подшипника. Техника работ показана на видео:
Большие ножи можно сделать из стенок подшипника, предварительно распилив их и сковав вместе.
Когда ковка завершена, клинок стабилизируют, поместив его в очаг горна и оставив остывать там.
Планируя поковку ножа, можно изначально потренироваться на различных материалах. Например, можно взять полосу рессорной стали 65Г. Из нее также можно сделать хороший образец рабочего клинка, так как такая сталь довольно высокого качества, а ее объема будет достаточно для изготовления десятка различных ножей.
Некоторые специалисты рекомендуют перед поковкой ножей набить руку на ковке подков! При отработке такой технологии тренируются все те же кузнецкие приемы.
Попрактиковавшись, можно выковать практически любой клинок.
Если Вы можете поделиться своим опытом, оставьте свои комментарии или примите участие в обсуждении этого материала. Расскажите, какие материалы и приемы вы использовали при поковке ножей, а также какие типы приходилось изготавливать.
wikimetall.ru
Кованый или прокатный и другие заблуждения
В основе всех рассуждений на тему какой нож лучше — из кованой стали или из прокатной, лежит прочный стереотип, что при ковке сталь улучшается, а при прокате, должно быть, портится или как минимум не улучшается. Иногда еще можно услышать фразы «штампованная сталь» или «штампованный нож», которым придается крайне негативный оттенок и воспринимается, как что-то заведомо некачественное, худшее, нежели столь благородно звучащее — «кованый нож».
Необходимо внести ясность, что на самом деле штампованная сталь сама по себе не существует отдельно от того или иного конкретного изделия, получаемого методом штамповки, а ножи как раз методом штамповки не производят вообще. Штамповка это процесс формовки материалов посредством давления штампом определенной формы. Но к клинкам ножей это не относится, потому что технологически нет нужды — нечего там штамповать. Про ширпотребные китайские кухонники мы тактично не упоминаем, так как большинство из них всё-таки очень трудно называть полноценными ножами.
Если обобщить, именно клинок ножа, с его характерной формой и габаритами, может быть получен двумя способами:
1. Объемная горячая формовка из заготовки стали почти любой формы, то есть методом ковки, причем преимущественно ручной — молотком на наковальне. Это подразумевает случаи единичного производства клинков, когда над каждым из них работает кузнец с молотком и вручную формует клинок требуемого размера и конфигурации.
2. Резка. Начиная от человека с ножовкой по металлу, заканчивая лазерным станком с программным управлением. Осуществляется методом вырезания из заготовки заведомо плоской формы, которая в свою очередь может быть получена либо прокаткой, либо ковкой. Причем самое интересное, что на сегодняшний день практически любая кованая заготовка для будущего клинка производится методом ковки из стального прутка, который в свою очередь был получен опять же методом проката.
Так что такое кованая сталь и чем она отличается от не кованой, если всё равно изначально получается из прокатной?
Ясно, что нас интересует не просто технологическая разница, но различие результативное, по факту, чем так называемый «кованый нож» лучше ножа из прокатной стали? Ведь не даром можно слышать от многих производителей, что их ножи кованные, а потому заведомо лучшие. Без каких-либо объяснений и доказательств. И подавляющее большинство потенциальных покупателей замечательно подкупается подобными лозунгами, кстати так же, как и словом «булат». Производители это прекрасно осознают и пользуются ситуацией, а именно, отсутствием у покупателя понимания процессов, происходящих со сталью во время производства.
Чтобы разобраться во всей этой путанице, важно обозначить главный момент: решающим является вопрос терминологии. Не определившись с терминами, трудно что-либо согласовать и уложить по полкам. Жонглируя словами «простой, булатный, порошковый, кованый, прокатный» и их сочетаниями можно вводить человека в заблуждение бесконечно долго. Это фразы, которыми оперируют коммерчески продвинутые производители, сути происхождения стали они не отображают, и о свойствах каждого конкретного ножа они ничего не говорят.
Поэтому необходимо чётко разделить понятия: что такое нож кованый и нож не кованый.
Часть 1. Ковка, как необходимость.
Кованый нож, а точнее говоря, кованый клинок — это когда из заготовки стали, неважно какой формы, человеком вручную формуется контур и геометрия клинка, вытягивается хвостовик, оттягиваются будущие спуски. Применяется такой метод только в условиях единичного производства ножей одним мастером или немногочисленной группой мастеров. С точки зрения целесообразности метод обоснован в случаях:
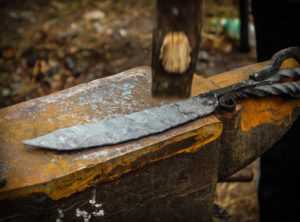
1. Если изначальная заготовка стали не совсем подходящей формы. Например, из круглого подшипника одним только способом резки клинок не получить.
2. Ковка клинка в чистовой размер как способ экономии материала. Это объединяет как древних кузнецов, которые знали истинную цену сырью для производства оружия и инструмента, так и современных мастеров, бережливо кующих клинки из полосы дорого купленной стали, просто потому что отрезать лишнее и выбрасывать — расточительно.
3. Когда усиленная деформация осуществляется с целью повлиять на некоторые составляющие структуры стали. В частности, если стоит задача несколько раздробить плотные скопления карбидов в сталях с их высоким содержанием и неравномерным распределением.
Кстати, такой подход дробления твердых фаз принципиально характерен вообще для производства сталей с изначально высоким содержанием крупных карбидов и их скоплений — быстрорежущих, некоторых штамповых сталей (не путать слова «штамповый» и «штампованный»). Подробнее о ножевых сталях и их особенностях можно прочитать в этой статье.
После непосредственного производства, то есть выплавки, в своем самом первичном виде эти стали содержат настолько крупные скопления карбидов, что их подвергают прокату и ковке, то есть сильной горячей деформации, до тех пор, пока карбиды не измельчатся до определенного размера. Явление называется карбидной неоднородностью и имеет несколько чётко обозначенных степеней.
В противном случае, к примеру, быстрорежущая сталь с недостаточно раздробленными включениями карбидов считается бракованной. Поскольку крупные карбидные включения являются очень твердыми и хрупкими, то зуб пилы, фрезы, или сверло, на режущую кромку которого попадает такой нежелательный фрагмент, обречено на неизбежное выкрашивание. Если проводить аналогию с ножом, режущая кромка которого геометрически отличается от режущей кромки фрезы, как яхта от ледокола, то для тонкой и острой РК ножа наличие огромных, твёрдых и хрупких элементов в структуре сказывается еще более плачевно.
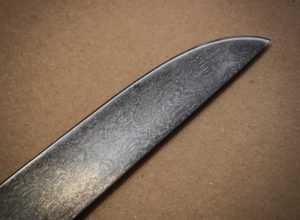
Это к слову о так называемых «булатах», как исторических, так и новодельных, у которых степень карбидной неоднородности настолько высока, что густые скопления карбидов в виде различных узоров можно без труда разглядеть невооруженным глазом на расстоянии вытянутой руки. И это в противовес не имеющим никакого узора современным порошковым быстрорежущим сталям, в составе которых содержание сверхтвёрдых карбидов тугоплавких металлов очень велико, но они имеют минимально возможный размер и максимальное распределение, что позволяет таким сталям демонстрировать колоссальные результаты по удержанию остроты режущей кромки.
Часть 2. Реалии ножевого производства.
Ручная ковка стали, в комплексе с другими циклами термообработки, нацеленными на создание необходимой структуры — это метод, позволяющий получить качество ножа, отличное от качеств, свойственных подавляющему большинству других ножей из той же самой стали, но производимых на потоке, к которым применяются стандартные режимы ТО.
Для неискушенных пользователей, разница в стоимости между такими ножами зачастую перекрывает разницу в реальных преимуществах. Поэтому в условиях множественного производства ножей ручная ковка клинков и применение специальных режимов термообработки являются необоснованными с точки зрения экономики предприятия, выпускающего ножи в большом количестве.
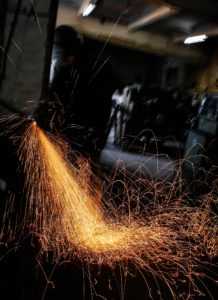
Все так называемые «кованые ножи» в условиях современного поточного производства — это когда из прокатного прутка методом ковки на пневмомолоте получают поковку-полосу, из которой потом болгаркой вырезают клинки. После чего, как правило, сразу следует закалка, то есть о какой-либо предварительной термообработке, нацеленной на подготовку структуры к закалке, устранение структурных напряжений после ковки, а так же уменьшение зерна металла, речи не идёт.
Соответственно, такие клинки определенно будут иметь более низкие свойства, чем вырезанные из полос, но прокатанных по технологическим нормам и отожженных сразу на металлургическом заводе, минуя стадию расковки на пневмомолоте кузнецом, квалификация которого всегда остается загадкой для покупателя.
И хотя в каталогах некоторых местных производителей сегодня можно встретить модели ножей со следами, дескать, «ручной ковки», не обольщайтесь — от того что по заранее вырезанной пластине для сомнительной красоты рельефа немножко постучали молотком за пару бестолковых нагревов, сталь лучше, увы, не становится. Яркий пример тому — любой нож из стали 9ХС, сделанный в Ворсме, причем не важно в какой из тамошних фирм.
И тут назревает самый важный вопрос: так от чего же всё-таки сталь приобретает лучшие свойства?
Ответ простой: сталь становится лучше от применения осознанной целевой качественной термообработки. Важно понимать, что качественная термообработка это не просто хорошая закалка клинка с правильных температур и в нужной среде, но весь комплекс мероприятий, связанных с температурным воздействием на сталь, в том числе это относится и к горячей деформации стали. Причём без громадной принципиальной разницы, происходила ли она под воздействием динамической нагрузки, то есть с ударами молота, либо под более плавным воздействием — при прокате в стане. Поэтому попытка производителя на словах выдать якобы «кованый» нож в качестве заведомо лучшего, нежели прокатный, должна подвергаться здравому скептицизму и вызывать встречные вопросы с просьбой описать технологическую последовательность производства этих хвалёных кованых ножей.
Однако, в жизни между двумя методами горячей деформации, ковкой и прокатом, разница всё же есть. И очень часто она серьёзно сказывается на качестве обрабатываемой стали, а значит и на качестве конечного изделия.
Часть 3. Человеческий фактор.
Отличие проката в стане на металлургическом заводе от ковки кузнецом на пневматическом молоте — в присутствии человеческого фактора.
Прокат стали это автоматизированный процесс, где все стадии проходят в обусловленных технологических рамках: температурный режим, направление деформации, степень деформации. Всё это точно рассчитано и безукоризненно осуществляется механикой и автоматикой. На выходе из прокатного стана получаются изделия необходимой формы, соответствующие всем требованиям по качеству. Сталь проходит ОТК, где наличие и без того маловероятных структурных неоднородностей, трещин и прочих дефектов, выявляется и забраковывается, то есть некачественный продукт не выходит из стен производства и отправляется на переплавку.
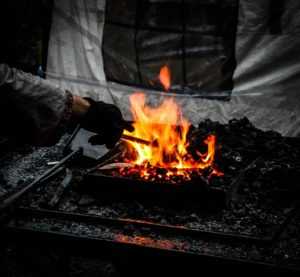
Совсем другое дело, это горячая деформация в кустарных условиях, тем более с применением промышленного оборудования, такого как тяжёлые пневматические молоты. Здесь главный фактор, влияющий на конечный результат — квалификация оператора молота и горна, то есть кузнеца. Потому что один кузнец выполняет функцию инженера, технолога, наладчика, мастера и контролера ОТК. И только от присутствия комплексных знаний и личной ответственности у конкретного кузнеца зависит, насколько качественной будет сталь, к которой он применял горячую деформацию.
Сталь имеет свойство необратимо разрушаться при применении к ней неправильных температурных и деформационных режимов. То есть, чтобы качественно расковать сталь, нужно объективно понимать и учитывать огромное количество статичных, а так же изменяющихся во времени параметров.
Само собой, любой уважающий себя кузнец обязан знать «на зубок» тепловые режимы для большинства марок стали. Должен относительно точно определять температуру металла по цвету нагрева и филигранно управляться с огромной ухающей махиной. Но не каждому дано в абсолюте чувствовать металл и не позволять применять степень деформации, превышающую критическую для каждой конкретной стали и конкретной температуры нагрева. Плюсом к этому идут другие негативные и часто неотъемлемые факторы, такие как спешка, в следствие желания охватить большой объем работы в кротчайший срок, личная безответственность по отношению к качеству выпускаемой продукции, неправильная организация рабочего пространства, иные отвлекающие явления или искажающие поступающую информацию о состоянии процесса, и т.д.
Часть 4. Качество ковки.
Упоминая о таких распространенных «залипонах» в околоножевой среде, как «ковка упрочняет сталь» или «ковка делает сталь плотнее», необходимо внести ясность, что всё-таки упрочняет сталь закалка, а не ковка. Это факт, применяемый во всех отраслях построения конструкций из металла. Ковка, как и прокат — это способ формовки изделий, а не упрочнения стали. Ковка так же и не уплотняет сталь, но за то, вопреки всем стереотипам, запросто может снизить её плотность. Конечно, когда речь идет о ковке пористых отливок металла, само собой ковка его уплотняет, а если быть точнее, приводит плотность к нормальному для данного металла значению, потому что в отлитом металле всегда будут присутствовать поры и прочие неоднородности, снижающие нормальную плотность. И если сталь, в частности, в виде заводского кругляка, уже имеет нормальную плотность, можно ли её повысить ковкой? Увы, это всего лишь расхожее заблуждение. А вот снизить её, за счет образования множественных микротрещин в объеме стали, можно запросто.
Существуют определенные пределы приложения нагрузки на горячий металл, переходя которые можно ощутимо изменить внутреннюю целостность заготовки. Высокоуглеродистая сталь не терпит неправильного приложения ударов огромной силы, которые зачастую исходят от больших пневмомолотов, даже несмотря на соблюдение интервала ковочных температур. А в сталях с определенной степенью легирования, если их деформировать, не обращая внимание, например, на подстуживание, можно получить не то чтобы структурные микро-разрушения, но и вполне себе ощутимые трещины. Перегрев любой стали тоже ведет к негативным, а иногда и необратимым разрушительным последствиям. По этому, с точки зрения статистики, гораздо больше доверия заводскому прокатному стану, нежели непонятному кузнецу, работающему на огромном пневмомолоте.
5. Выбор.
Критерий, по которому можно что-либо определить, только один — практика. Если тот или иной кузнец или производитель ножей утверждает, что сталь в его ножах хорошо откована, не имеет дефектов, а это касается не только видимых глазу трещин, но и таких структурных изъянов, которые можно наблюдать только в микроскоп или с помощью рентгена, то опровергнуть или подтвердить его слова можно только лабораторными анализами структуры стали, либо её тестированием в полевых условиях, что в случае с готовым ножом является самым верным способом выяснить все его качества. Тем более, что полдела иметь не испорченную сталь, но еще более важно её правильно закалить. Поэтому, чтобы покупка ножа не превращалась в лотерею, прежде всего необходимо быть уверенным в производителе и его отношении к своему делу.
В целом же хочется посоветовать выбирать тот или иной нож не только по критериям, которые старается в первую очередь обозначить или даже навязать сам продавец, но и обращать внимание на другие, куда более значимые аспекты, говорящие сами за себя. Это касается как ножей, так и поведения самого продавца, манеры позиционирования себя и своей продукции. В первую очередь следует обращать внимание на качество исполнения ножа, не только внешнее, но и с точки зрения соответствия конструкции ножа задачам, предполагаемым к выполнению. И конечно же, всегда нужно критически относится к любым громким заявлениям, анализировать поступающую информацию, искать другие источники, сравнивать, делать выводы. Тогда у вас будет гораздо меньше шансов купить недобросовестно сделанный нож.
Симонов Кирилл
uralmade.com
всё о ножах: Сталь для ковки ножей
Технические характеристики ножа во многом определяются материалом, который применяется для ковки клинка. Зная состав металла, уже можно предположить, какими из требуемых качеств будет обладать изготовленный из нее нож. Основным элементом, присутствующим во всех видах стали, придающим клинку крепость и твердость, является углерод. Свою роль в придании металлу тех или иных качеств выполняют различные добавки и примеси, в числе которых:
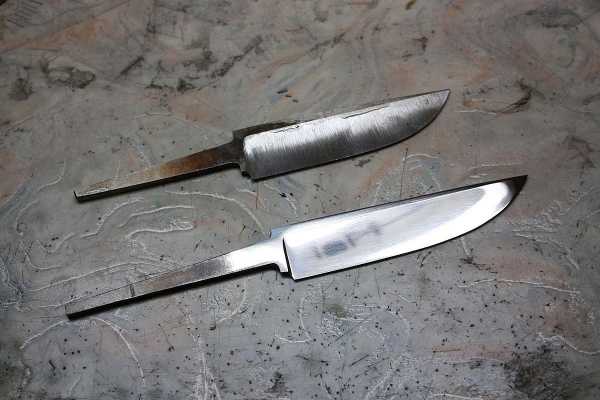
- магний, придающий металлу зернистую структуру и повышающий его прочность и износостойкость;
- кремний, увеличивающий твердость сплава;
- хром, повышающий износостойкость, обеспечивающий устойчивость к коррозии и способность к закаливанию;
- молибден, предотвращающий ломкость и хрупкость клинка ножа, придавая ему стойкость к нагреву;
- никель, повышающий прочность металла;
- вольфрам, препятствующий износу клинка: в комбинации с хромом или молибденом увеличивает режущие свойства лезвия;
- ванадий, значительно улучшающий износостойкость и прочность сплавов, позволяющий изготавливать лезвия большой остроты.
В более общем понимании, сталь для ковки ножей бывает: черной и нержавеющей. Но если за изделием не ухаживать должным образом, любой сплав может быть подвержен коррозии. Нержавеющую сталь ковать очень тяжело. Кованными чаще всего бывают клинки из черного металла.
Ковка ножей из дамасской стали
С давних времен высоко ценятся кованные ножи из дамасской стали. Славу им принесли их превосходные режущие качества. А отличают их характерные разводы на клинке, складывающиеся в причудливые узоры. Образуются они в результате видимого сочетания в одном изделии различных по своему составу полос металла.
Процесс изготовления дамасской стали довольно не простой, и требует мастерства. В современных условиях для этого предлагается специальный пакет, состав которого представлен девятью полосами «мягкого» и десятью полосами «инструментального» металла. Сложив заготовку из полос одинаковых размеров, их требуется сварить при помощи высокотемпературного воздействия. Следуя двум особым правилам, достигнуть результата будет проще. Итак:
- чтобы визуально правильно оценить нагрев металла, процесс следует проводить в полумраке, лучше не в дневное время: если слои не прогреть, как следует, то они не сварятся, а при слишком высоких температурах перегретая заготовка может раскрошиться;
- обычная поваренная соль, если в нее поместить пакет для сварки дамасской стали, расплавившись, не дает металлу при нагревании гореть, не мешая при этом самому процессу обработки: плавка кристаллов соли сигнализирует о предельном значении температур, при котором стоит производить кузнечную сварку.
Далее следует этап вытягивания стальной заготовки. Легче и качественнее ковка осуществляется при помощи кузнечного молота, чем обычным ручным инструментом. Его постоянные, часто повторяющиеся удары быстрее обрабатывают форму, благодаря чему она без задержек возвращается в печь и меньше подвергается температурным скачкам. По окончании ковки дамасская сталь проходит процесс закаливания: при опускании в воду на клинке появляются характерные полосы и волны, за что такие изделия ценятся среди знатоков и коллекционеров.
Видео ручной ковки ножа из дамасской стали
Чтобы лучше представить себе все этапы и последовательность действий, которые необходимо произвести для того, чтобы изготовить столь уникальное изделие, как нож из дамасской стали, в сети Интернет выложены видеоматериалы, подробно и наглядно описывающие все процессы. На них четко показано, что заготовка должна располагаться на определенном расстоянии от пламени в печи, которое часто отмечено специальной отметкой. Класть ее следует в горизонтальном положении, периодически переворачивая, но ни в коем случае не на ребро, поскольку это может только повредить изделие. Для лучшего скрепления слоев прогретую заготовку рекомендуется время от времени простукивать молотком – как на видео.
Ковка ножа из дамасской стали обязательно включает в себя увеличение слоев за счет так называемого «скручивания» заготовки в процессе ее сварки. Чем больше сварок прошел дамасский нож при изготовлении, тем больше слоев мягкого металла прошивают твердые сорта стали, обеспечивая лучшие качественные характеристики самого изделия: легкость, прочность и остроту. Опытный мастер в состоянии самостоятельно определить сколько раз следует скрутить будущий нож для обеспечения оптимального смешивания слоев без вреда для его клинка.
Традиции производства русского булата
Определение дамасская сталь со временем вошло в общее понятие булатной стали — очень популярного материала для ножей ручной ковки. Хотя между этими двумя сортами металлов существуют принципиальные различия. По своему химическому составу булат представляет собой высокоуглеродистую сталь без каких-либо специальных примесей. По количественному содержанию углерода он близок к чугуну. Но по своим физическим свойствам металл проявляет способность к ковке, как у низкоуглеродистых сталей. Кованные булатные ножи после закалки значительно превосходят последние по твердости.
Многие исторические факты указывают на то, что на Руси существовало производство булата. За вековую историю технология его изготовления претерпела прогрессивные изменения, но не была утеряна. Многие современные материалы для ножей превосходят булатную сталь, но он по-прежнему являются непревзойденным образцом металла. До наших дней сохранился булатный клинок, изготовленный в середине 19 века на Златоустовском производстве: он на лету разрезает платок из тонкого газа, перерубает гвозди и гнется в дугу.
Процесс изготовления и обработки таких образцов – настоящее искусство, которым владеют истинные мастера. Булатная сталь образуется при введении в сплавы железа значительного количества углерода (до 1,5%). Процесс медленного охлаждения приводит к распределению во взвешенном состоянии в объемах обычной стали соединений железа, сильнонасыщенных углеродом, так называемого цементита. Прослойки цементита обволакиваются постепенно остывающим мягким железом. В результате, металл приобретает твердость с сохранением вязкости и упругости, которых лишена обычная сталь.
Ковка ножей из булата должна производиться предельно аккуратно и осторожно. Чтобы не повредить прослойки хрупкого цементита, такие изделия обрабатывают ударами легкого молота, в ходе многократного нагревания до красного каления. Переход за критическую температуру может привести к утрате металлом своих ценных качеств и специфичного рисунка.
По цвету, такие клинки бывают черные, серые и бурые. Качество изделия тем выше, чем темнее металл, и более контрастен рисунок на нем. Разделяют несколько разновидностей узоров на булатных ножах:
- полосатый, образованный параллельными прямыми линиями;
- струйчатый и волнистый, в результате чередования прямых и кривых линий;
- сетчатый – при пересечении коротких прямых и завитых линий;
- коленчатый в виде повторяющегося замысловатого рисунка по всей поверхности клинка.
Несколько комментариев по тестированию ножей из дамасской стали и булата
Острота лезвия – главное достоинство любого клинка. Кованные ножи из дамасской стали или булата можно заточить, добившись неправдоподобной остроты, которая сохраняется надолго. Как показывает практика, заточенные до остроты бритвы, они сберегают свои режущие свойства при многократных применениях. Лезвие ножей имеет свойство самозатачиваться, вследствие таких качеств данных сортов стали, как высокая твердость, упругость и вязкость.
Не стоит придерживаться мнения, что образцы из дамасской стали по причине их подверженности коррозии способны вызвать интерес только у коллекционеров. По мнению профессионалов, они вполне могут использоваться по назначению. Если не лениться ухаживать за любимым инструментом, к примеру, при стандартных охотничьих операциях, дамасский нож, как обладающий высокой стойкостью режущей кромки, не уступает булатному. При всей его уникальности, им можно и хлебушек резать, и гвозди стругать. В конечном итоге, любому ножу покупатель находится.
«Сталь для ковки ножей» прочитали 4340 раз(а)
top-nozhi.ru
Ножевые стали | Кузница Коваль
При выборе охотничьих, туристических, кухонных и ножей для повседневного использования (EDC), топоров или мачете, следует поближе познакомиться с материалом для изготовления режущей части этих изделий.
Очень важно знать, какими свойствами обладает марка стали, который используется в изделии. К таким свойствам относятся, в первую очередь, упругость, вязкость, способность держать заточку, устойчивость к коррозии, твердость и способность к доводке режущей кромки. При этом не следует также упускать из виду такие факторы, как пригодность стали для обработки и ее стоимость.
Ни одна сталь не может объединять в себе все положительные свойства. Углеродистая сталь, например, за счет мелкозернистой структуры легко затачивается, но при этом не очень устойчива к коррозии. Клинки из стали, изготовленной с применением метода порошковой металлургии, мало подвержены коррозии и хорошо сохраняют режущие свойства, но одновременно трудно поддаются доводке режущей кромки, поэтому процесс обработки такой стали очень трудоемок и стоит довольно дорого.
Стали, используемые для производства ножей, можно грубо разделить на две группы: углеродистые и легированные стали.
Углеродистые стали
В принципе, любая сталь, предназначенная для изготовления ножей, должна поддаваться закалке, для чего содержание углерода в ней должно быть не менее 0,5%. При содержании углерода свыше 1,7% сталь уже не поддается обработке ковкой. В углеродистых сталях практически отсутствуют другие составные элемента сплава, как, например, марганец, хром, ванадий, молибден.
Одним из свойств углеродистой стали является ее простота при термической обработке, то есть, имея относительно широкий температурный диапазон нагрева, эта сталь легко «прощает» погрешности мастера в процессе ковки и закалки. Углеродистая сталь хорошо поддается различным видам обработки в не закаленном состоянии (опиливание, сверление, шлифовка и т.д.), кроме того, легко затачивается. Благодаря мелкозернистой структуре карбидов железа лезвие из такой стали в результате заточки может быть очень острым.
Основным недостатком углеродистой стали является отсутствие коррозионной стойкости, что, правда, можно свести до минимума с помощью полировки поверхности изделия до блеска и, конечно, тщательного ухода. На практике это означает следующее: после эксплуатации ножа, его клинок необходимо очистить от грязи и слегка смазать маслом. Но даже самый лучший уход не может предотвратить образование на поверхности углеродистой стали серого налета и пятен, если клинок ножа входит в контакт с кислотами, например, с фруктовой кислотой при резке томатов или яблок, а также при соприкосновении с жирными кислотами, например, при резке жареного мяса.
Легированные стали
Легированные инструментальные стали являются идеальным материалом для изготовления ножей.
Все легированные стали имеют следующие положительные свойства: устойчивость к коррозии (если содержание хрома свыше 13%), твердость и способность сохранять режущие свойства. Выбор правильной стали зависит, в первую очередь, от того, для каких целей предназначен будущий нож.
Стали, изготовленные метолом порошковой металлургии (ПМ), отличаются значительно более высокой износостойкостью по сравнению со стандартными сталями, кроме того, они прекрасно поддаются закалке и одновременно сохраняют хорошую вязкость — три свойства, которые можно только пожелать ножевой стали. В последнее время эти стали все больше используются в ножевом производстве.
Технология изготовления стали с применением порошковой металлургии достаточно дорогостоящая. В ходе технологического процесса расплавленные составные элементы сплава распыляются в вакууме ИЛИ инертном газе, после чего, находясь в тестообразном состоянии, спрессовываются под высоким давлением и при высокой температуре. Благодаря этому процессу элементы сплава легко соединяются друг с другом, тогда как просто в расплавленном состоянии и при достаточно высокой концентрации смешать их уже невозможно. Это можно сравнить с солью и водой: соль хорошо растворяется в том или ином объеме воды до определенного предела насыщения; если добавлять соль далее, то растворяться она уже не будет. Кроме того, в ходе данного процесса твердые карбиды принимают форму мелких шариков почти одинакового размера, поэтому благодаря мелкозернистой структуре сталь, изготовленная с помощью данной технологии, хорошо полируется.
За счет большой вязкости и высокого сопротивления разрыву сталь ПМ имеет больший предел прочности лезвия на излом, чем обычные марки сталей. Это свойство позволяет подвергать такую сталь более высокой степени закалки, а это значит, что лезвие ножа может быть тоньше.
Совершенно очевидно, что сталь ПМ за счет ее трудоемкого производства дороже, чем сталь, созданная обычным литьем.
Вязкость и износостойкость данной марки стали в значительной степени затрудняют ее обработку, что приводит к повышенному износу инструментов и абразивных лент. Все эти факторы, соответственно, сказываются на стоимости ножа, изготовленного из этой супер стали.
С какой целью к железу добавляются легирующие элементы? Объясняется это довольно просто: железо подвергается закалке только в соединении с углеродом, поэтому, для того чтобы получить ту или иную марку стали, к железу добавляется углерод в различных количествах.
Существует ряд элементов, которые облагораживают сталь и коренным образом меняют ее свойства.
Углерод придает стали жесткость и вместе с железом и другими элементами образует карбиды — чрезвычайно твердые метало-углеродистые соединения.
Хром придает сплаву коррозионную стойкость: при содержании хрома не менее 13% сталь становится нержавеющей. Кроме того, хром повышает твердость и износостойкость стали.
Марганец придает материалу клинков зернистую структуру, которая, в свою очередь, способствует прочности ножа или инструмента из стали.
Кремний, также как и марганец, при ковке клинка ножа используется для придания ему крепости.
Ванадий, так же, как и тантал, никель, молибден, кобальт и вольфрам, повышает износостойкость и жесткость стали.
Ниже приводится подробное описание популярных марок стали, используемых для производства клинков туристических и охотничьих ножей, топоров, тяпок и мачете, а также складных ножей.
Российские стали для производства ножей:
Сталь Х12МФ. Из стали изготавливают профилировочные ролики сложных форм, секции кузовных штампов сложных форм, сложные матрицы при формовке листового металла, эталонные шестерни, накатные плашки, волоки, матрицы и пуансоны вырубных просечных штампов со сложной конфигурацией рабочих. Сталь Х12МФ хорошо зарекомендовала себя в изготовлении клинков для ножей. Неприхотливая, но удобная в работе сталь для изготовления ножевого инструмента. Сталь х12МФ отлично держит заточку, обладает высокой прочностью, хорошо держит режущую кромку. При попадании в агрессивную среду может покрыться налетом или на клинке ножа могут появятся темные пятна, поэтому нож из стали Х12МФ требует ухода. Нужно отметить, что многие производители льют булат на основе Х12МФ.
Состав стали марки Х12МФ: Углерод (С) 1,45 – 1,65 %, Марганец (Mn) 0,15 – 0,45 %, Хром (Cr) 11 – 12,5 %, Кремний (Si) 0,10 – 0,40 %, Молибден (Мо) 0,4 – 0,6 %, Ванадий (V) 0,15 – 0,3 %, Никель (Ni) 0,35 %, Фосфор (Р) 0,03 %.
Типичная твердость стали для ножей из Х12МФ по шкале Роквелла: 60 – 62HRc.
Аналоги стали для ножей марки Х12МФ в других странах: SLD (Япония), X155CrMo12.1 (Германия), SKD-11 (Швеция), D2 (США).
Посмотреть ножи из Х12МФ
Сталь 95Х18. 95Х18 — высоколегированная нержавеющая сталь для ножевого производства, обладающая высокой твердостью, стойкостью режущей кромки, высокой коррозионной стойкостью. Сталь 95Х18 считается одним из лучших материалов для изготовления клинковых изделий. В целом — одна из лучших сталей, применяемых для производства ножей по соотношению цена-качество. Промышленное предназначение стали 95Х18 — детали, к которым предъявляются требования высокой прочности и износостойкости и работающие при температуре до 500С или подвергающиеся действию умеренных и агрессивных сред.
Состав стали марки 95Х18: Углерод (С) 0,90 – 1,00 %, Марганец (Mn) 0,80 %, Хром (Cr) 17 – 19 %, Кремний (Si) 0,80 %, Фосфор (Р) 0,025 %.
Типичная твердость стали для ножей из 95Х18 по шкале Роквелла: 57 – 59Hrc.
Аналоги стали для ножей марки 95Х18 в других странах: AUS-8 (Япония), X90CrMoV18/1L4112 (Германия), 123C26 (Швеция), 440B (США).
Посмотреть ножи из 95Х18
Сталь 110Х18МШД. Это нержавеющая сталь мартенситного класса. Российская сталь производимая методом электрошлакового (ЭШП) и вакуумно-дугового (ВДП) переплава, с соответствующей маркировкой: 110Х18М-Ш и 110Х18М-ШД. Эта сталь нашла применение в подшипниках специального назначения и в ответственном хирургическом инструменте, так как к ней предъявляются требования высокой прочности и износостойкости. Наличие вредных примесей, таких как сера и фосфор меньше по сравнению с другими сталями для ножевого производства. При использовании стали 110Х18 в клинках ножей достигается превосходное сочетание режущих и прочностных свойств и коррозионной стойкости.
Состав стали марки 110Х18МШД: Углерод (С) 1,10 – 1,20 %, Марганец (Mn) 0,10 – 0,50%, Хром (Cr) 16,5 – 18 %, Молибден (Мо) 3,0 %, Никель (Ni) 0,5 %.
Типичная твердость стали для ножей из 110Х18МШД по шкале Роквелла: 58 – 61Hrc.
Аналоги стали для ножей марки 110Х18МШД в других странах: SUS440C (Япония), X105CrMo17/1,4125 (Германия), 19C27 (Швеция), 440C Crusible Metals (USA).
Посмотреть ножи из 110Х18МШД.
Сталь 65X13. Высоколегированная коррозионно-стойкая сталь. Весьма распространенная сталь для производства недорогих ножей, режущего инструмента, кухонных ножей, пил, съемных лезвий, скальпелей, лезвий бритв. Изначальное её предназначение — режущий инструмент, кухонные ножи, пилы, съёмные лезвия, скальпели, лезвия бритв. Поскольку из неё часто делают скальпели и другие медицинские инструменты, её ещё часто называют «медицинской». В общем, сталь 65Х13 — достаточно неплохой вариант для недорогого рабочего и подарочного ножа.
Состав стали марки 65X13: Углерод (С) 0,65 %, Марганец (Mn) 0,40 %, Хром (Cr) 13 – 15 %, Кремний (Si) 0,30 %, Молибден (Мо) 0,02 – 0,1 %, Ванадий (V) 0,02 – 0,10 %, Никель (Ni) 0,25 – 0,40 %.
Типичная твердость стали для ножей из 65X13 по шкале Роквелла: 56 – 58HRc.
Аналоги стали для ножей марки 65X13 в других странах: 440A (США), AUS6 (Япония), X55CrMo14 (Германия), AEB-L (Швеция).
Посмотреть ножи из 65Х13.
Сталь 9ХС. Инструментальная легированная сталь российского производства, используется для изготовления различного рода инструментов. Из стали 9ХС производят: сверла, развертки, метчики, плашки, гребенки, фрезы, машинные штемпели, клейма для холодных работ. Ответственные детали, материал которых должен обладать повышенной износостойкостью, усталостной прочностью при изгибе, кручении, контактном нагружении, а также упругими свойствами. Сталь 9ХС относительно недавно сыскала большую популярность в охотничьих ножах ручной ковки. Нож из кованой стали 9ХС обладает хорошими режущими качествами и отлично держит заточку.
Состав стали марки 9ХС: Углерод (С) 0,85-0,95 %, Марганец (Mn) 0,30-0,60 %, Хром (Cr) 0,95 – 1,25 %, Кремний (Si) 1,20-1,60 %, Молибден (Мо) 0,20 %, Ванадий (V) 0,15 %, Никель (Ni) 0,35 %, Фосфор (Р) 0,03 %, Вольфрам (W) 0,2 %
Типичная твердость стали для ножей из 9ХС по шкале Роквелла: 60 – 63HRc.
Посмотреть ножи из 9ХС.
Сталь ХВ5. Хромовольфрамовая инструментальная легированная сталь. ХВ5 – одна из самых твердых инструментальных сталей. Из-за повышенной твердости ХВ5 называют «алмазной сталью». Применяется сталь ХВ5 для инструментов, работающих с малыми скоростями резания при обработке металлов повышенной твердости (отбеленного чугуна, стекла, фарфора), а также при срезании стружки малого сечения. Кроме того из этой стали получаются прочнейшие ножи , которые по свои характеристикам, режущим свойствам и твердости оставляют далеко позади ножи из других углеродистых и легированных сталей. При правильной термообработке клинок из алмазной стали может иметь твердость до 69-70 HRc.
Состав стали марки ХВ5: Углерод (С) 1,3-1,35 %, Марганец (Mn) 0,10-0,30 %, Хром (Cr) 0,4 – 0,7 %, Кремний (Si) 0,10-0,30 %, Ванадий (V) 0,2 %, Вольфрам (W) 5%
Типичная твердость стали для ножей из ХВ5 по шкале Роквелла: 63 – 67HRc.
Посмотреть ножи из ХВ5.
Сталь У10. Инструментальная углеродистая сталь. Используется для производства инструмента, работающего в условиях, не вызывающих разогрева режущей кромки. Из стали У10 производят: метчики ручные, рашпили, надфили, пилы для обработки древесины, матрицы для холодной штамповки, гладкие калибры, топоры. Сталь У10 можно отнести к «классическому» клинковому материалу.
Состав стали марки У10: Углерод (С) 1,16 — 1,23 %, Марганец (Mn) 0,17 — 0,28 %, Хром (Cr) 0,2 %, Кремний (Si) 0,17 — 0,33 %, %, Никель (Ni) 0,2 %, Фосфор (Р) 0,02 %,
Типичная твердость стали для ножей из У10 по шкале Роквелла: 59 – 61HRc.
Посмотреть ножи из У10.
Сталь У8. Инструментальная углеродистая сталь. Используется для производства инструмента, работающего в условиях, не вызывающих разогрева режущей кромки. Из стали У8 производят: фрезы, зенковки, стамески, долота, пилы продольные и дисковые, накатные ролики, керны, отвертки, комбинированные плоскогубцы, боковые кусачки, топоры. Сталь У8, как и другие марки стали У можно отнести к «классическому» клинковому материалу.
Состав стали марки У10: Углерод (С) 0,76 — 0,83%, Марганец (Mn) 0,17 — 0,28 %, Хром (Cr) 0,2 %, Кремний (Si) 0,17 — 0,33 %, %, Никель (Ni) 0,2 %, Фосфор (Р) 0,02 %,
Типичная твердость стали для ножей из У10 по шкале Роквелла: 58 – 60HRc.
Посмотреть ножи из У8.
Сталь 65Г. Пружинно-рессорная сталь, легированная марганцем. Из стали 65Г производят: пружины, рессоры, упорные шайбы, тормозные ленты, фрикционные диски, шестерни, фланцы, корпусы подшипников, зажимные и подающие цанги и другие детали, к которым предъявляются требования повышенной износостойкости, а также детали, работающие без ударных нагрузок. Сталь 65Г не стойка к коррозии, недолго держит режущую кромку, но обладает высокой ударной вязкостью. В основном из этой стали изготавливают метательные ножи.
Состав стали марки У10: Углерод (С) 0,62 — 0,7 %, Марганец (Mn) 0,9 — 1,2 %, Хром (Cr) 0,25 %, Кремний (Si) 0,17 — 0,33 %, %, Никель (Ni) 0,25 %, Фосфор (Р) 0,02 %,
Типичная твердость стали для ножей из 65Г по шкале Роквелла: 55 – 58HRc.
Аналоги стали для ножей марки 65Г в других странах: 1066, 1566, G15660 (США), 66Mn4, Ck67 (Германия).
Посмотреть ножи из 65Г.
Импортные стали для производства ножей:
Сталь UDDEHOLM ElMAX. Elmax Superclean — порошковая инструментальная коррозионно-стойкая сталь концерна Bohler Uddeholm. Сталь ELMAX довольно давно присутствует на рынке и достаточно популярна при производстве клинков для ножей. По стойкости эта сталь для ножей несколько уступает стали M390 и приближается по свойствам к стали CPM S30V. Elmax безусловно можно отнести к передовым мировым сталям, изготовляемым методом порошковой металлургии. Имея повышенную чистоту, вязкость и карбиды небольшого размера сталь Elmax прекрасно держит заточку, устойчива к агрессивным средам.
Состав стали марки ElMAX: Углерод (С) 1,72 %, Хром (Cr) 17,8 %, Кремний (Si) 0,8 %, Молибден (Мо) 0,99 %, Ванадий (V) 2,99 %, Никель (Ni) 0,15 %, Вольфрам (W) 0,11 %, добавки редкоземельных металлов.
Типичная твердость стали для ножей из ELMAX по шкале Роквелла: 60 – 61HRc.
Посмотреть ножи из ELMAX.
Сталь UDDEHOLM VANADIS 10. Vanadis 10 — известная порошковая сталь от концерна Bohler Uddeholm с высоким содержанием ванадия, обладающая уникальным сочетанием отличной абразивной износостойкости и хорошей устойчивости к образованию сколов. Эта сталь производится с использованием процесса порошковой металлургии, что обеспечивает очень низкое содержание неметаллических включений. Uddeholm Vanadis 10 обладает хорошей обрабатываемостью и полиpуемостью, что, в сочетании с хорошей pазмеpной стабильностью при термообработке, обеспечивает неоспоримые преимущества для изготовителей режущего инструмента.
Uddeholm Vanadis 10 — это сталь, легированная
хромом, молибденом и ванадием, и обладающая
следующими характеристиками: чрезвычайно высокой абразивной
износостойкостью, высокой прочностью на сжатие, очень хорошей сквозной пpокаливаемостью, хорошей вязкостью, очень хорошей стабильностью при закалке, хорошей устойчивостью к вторичному отпуску.
Ножи из Vanadis 10 отличает высокая стойкостью к абразивному воздействию, высокая ударная прочность и вязкость, повышенная устойчивостью к образованию трещин сколов и заминов. Режущая кромка клинка очень долго не садиться и нож отлично держит заточку.
Состав стали марки VANADIS 10: Углерод (С) 2,9 %, Хром (Cr) 8 %, Кремний (Si) 0,5 %, Молибден (Мо) 1,5 %, Ванадий (V) 9,8 %, Вольфрам (W) 0,33 %, добавки редкоземельных металлов.
Типичная твердость стали для ножей из VANADIS 10 по шкале Роквелла: 62 – 64HRc.
Посмотреть ножи из VANADIS 10.
Сталь BOHLER M390 MICROCLEAN. Это коррозионностойкая мартенситная хромистая сталь получаемая методом порошковой металлургии. Большое содержание маленьких хорошо диспергированных карбидов Cr и Vв основном материале, содержащем, по крайней мере 12% хрома, дает следующие преимущества: наивысшая коррозионная стойкость, оптимальная износостойкость, превосходная полируемость. Благодаря своему составу и технологиям порошковой металлургии ножи из стали Böhler M390 имеют очень агрессивный рез, высокую износостойкость и отличную коррозийную устойчивость.
Состав стали марки BÖHLER M390 MICROCLEAN.: Углерод (С) 1,9 %, Хром (Cr) 20 %, Кремний (Si) 0,7 %, Молибден (Мо) 1 %, Марганец (Mn) 0,3 %, Ванадий (V) 4 %, Вольфрам (W) 0,6 %, добавки редкоземельных металлов.
Типичная твердость стали для ножей из M390 по шкале Роквелла: 61 – 64HRc.
Посмотреть ножи из M390.
Сталь BOHLER N695. Это мартенситная, хромистая нержавеющая сталь с высокой твердостью, износостойкостью и хорошей коррозионной стойкостью. Сталь N695 производится с использованием электрошлакового переплава. Является хорошей сталью для ножей, которым необходимо иметь не только стойкую режущую кромку, но и способность выдерживать ударные и боковые нагрузки на поворот и на излом.
Содержание примесей и легирующих добавок в сплаве для ножей марки N 695: Углерод (С) 1,05%, Кремний (Si) 0,4 %, Хром (Cr) 17 %, Молибден (Мо) 0,5 %, Марганец (Mn) 0,4 %.
Типичная твердость стали для ножей из N695 по шкале Роквелла: 57 – 60HRc.
Аналоги стали для ножей марки N695 в других странах: 440C, Z100CD17, SUS 440C, X105CrMo17, 5618, 5630.
Посмотреть ножи из N695.
Сталь BOHLER K340. Холодноштамповая инструментальная сталь концерна Böhler Uddeholm. Производится с использованием метода электрошлакового переплава (ЭШП). ЭШП обеспечивает уменьшение количества микро и макро сегрегации, а также чистоту и гомогенность структуры. Преимущества стали K340: гомогенная структура по всему объему заготовки; равномерные и минимальные изменения размеров; высокая вязкость, обеспечивающая широкий спектр областей применения; повышенный предел прочности на сжатие, особенно важный для тяжелонагруженных инструментов; улучшенная обрабатываемость, благодаря гомогенной структуре.
Состав стали марки K340: Углерод (С) 1,1 %, Хром (Cr) 8,3 %, Кремний (Si) 0,9 %, Молибден (Мо) 2,1 %, Ванадий (V) 0,5 %, Марганец (Mn) 0,4 %, добавки редкоземельных металлов.
Типичная твердость стали для ножей из K340 по шкале Роквелла: 59 – 62HRc.
Посмотреть ножи из K340.
Сталь D2. Это высокоуглеродистая хромистая инструментальная штамповая сталь. Сталь D2 имеет высокую стойкость к износу, компрессионным нагрузкам и абразивным воздействиям. Это одна из лучших и известнейших мировых сталей для производства ножей. Из стали D2 изготавливают ножи известные кампании из США и Японии. Ножи из этой стали отлично держат режущую кромку и имеют высокую коррозионную стойкостью. После термообработки твердость клинка из стали D2 находится в пределах 60-62 HRC.
Ножи из D2 практически не ржавеют, но поскольку сталь немного не дотягивает до нержавеющей (от 13% хрома), рекомендуется протирать клинки ножей и не оставлять на долго во влажных местах.
Состав стали марки D2: Углерод (С) 1,55 %, Марганец (Mn) 0,35 %, Хром (Cr) 11 – 12,5 %, Кремний (Si) 0,45 %, Молибден (Мо) 0,8 %, Ванадий (V) 0,8 %.
Типичная твердость стали для ножей из D2 по шкале Роквелла: 59 – 62HRc.
Аналоги стали для ножей марки D2 в других странах: Х12МФ (Россия), SLD (Япония), X155CrMo12.1 (Германия), SKD-11 (Швеция).
Посмотреть ножи из D2.
koval-knife.ru
Какой тип стали лучший для меча?
Это достаточно распространенный вопрос среди новичков, «лучший тип» зависит от типа меча и от того, в каких целях его собираются использовать…
Нужно упомянуть, что присутствует ряд более важных факторов, чем сталь, из которой сделан меч ( например, качество ковки важнее чем тип стали, из которой сделан меч — меч из хорошо закаленного куска самой дешевой нелегированной углеродистой стали гораздо лучше, чем плохо закаленный меч из стали L6.
Но давайте не будем все усложнять!
Так-что вместо этого давайте спросим «какие типы стали в основном используются для ковки мечей — и какие у них сильные и слабые стороны»(конечно, когда они закалены как надо!)?
Нержавеющая сталь
Раньше почти каждый меч был сделан из нержавеющей стали. Теперь она используется только для дешевых декоративных мечей — и не просто так!
Мечи из нержавеющей стали(или любые другие мечи в длину свыше 12″) считаются слишком хрупкими для применения и ломаются очень легко (как было продемонстрировано на печально известном видео home shopping video ниже.
Как объяснить это с технической точки зрения — нержавеющая сталь «не ржавеет» из-за того что в ней содержится высокий процент хрома (более 11%), и когда клинок достигает в длину 12″(меч), связь между хромом и сталью ослабевает. Так-что место мечей из нержавеющей стали — на стенке.
Примечание: Есть исключения из этого правила. Мечи из нержавеющей стали могут быть использованы для практики бесконтактных форм.
нелегированная углеродистая сталь
Для хорошего меча ( естественно, закаленного как надо ) нелегированная углеродистая сталь подходит лучше всего! Но что это значит?
Когда углеродистая сталь используется для ковки мечей, которая обозначается несколькими цифрами : первые две — 10, потом идут цифры от 1 до 99 ( каждая цифра обозначает содержание 0.1% углерода в стали.
Например, сталь категории AISI 1045 содержат 0.45% углерода, 1060 — 0.60% и т.д.
Стали с содержанием углерода от 0.05 до 0.15% считаются низшей углеродистой сталью, с 0.16 до 0.29 — средняя сталь. Ни та ни другая для мечей не подходят, т.к сталь с содержанием углерода менее 0.40% не могут быть закаленны как следует.
Чаще всего для ковки мечей используются 3 типа углеродистой стали : 1045, 1060 и 1095. Эксперты утверждают, что идеальное содержание углерода в стали, пригодной для хорошего и прочного меча — от 0.5 до 0.7 %, однако сталь 1045,самая недорогая, также используется.
Углеродистая сталь 1045
Мечи из этого типа стали сделать легко и недорого ( как при ручной ковке, так и при прессинге и на станке ). Эта сталь может быть закалена, и требует минимум затрат стали.
Когда меч такой стали хорошо закален, он достаточно крепок. И если вы найдете недорогой меч, который помечен как «сделанный из высшей углеродистой стали», это скорее всего сталь 1045, и меч, сделанный на станке.
Углеродистая сталь 1060
Мечи из этой стали — это идеальной баланс между прочностью и гибкостью. Они так-же известны своей прочностью. Мечи COLD STEEL сделанны из стали 1060.
Мечи из 1060 стали очень популярны несмотря на то, что их сложнее ковать.
VIDEO: Cold Steel Demo
Пример того на сколько прочны мечи из 1060 стали.
1095 углеродистая сталь
Эта сталь очень жесткая, и если мечи из 1095 стали закалены не должным образом, могут возникнуть проблемы при контакте с ещё более жесткой поверхностью (например например при попадании по деревянному стенду).
Итак, сталь с высоким содержанием углерода позволяет создавать особенно острые мечи. Но в этом случае острота может стоить мечу прочности.
Конечно, это не значит, что мечи из 1095 стали — хрупкие! Но определенные преимущества в прочности у мечей, сделанных из стали с низким содержанием углерода, есть.
Мечи из 1095 стали имеют репутацию «относительно» хрупких, и ключевое слово здесь — относительно. Все зависит от того, для чего вам нужен меч.
Пружинная сталь
Существуют два нужных нам типа пружинной стали — 5160 и 9260.Так-же как и в углеродистой стали, в них содержится 0.60% углерода ( идеальный баланс между прочностью и гибкостью ). Когда такая сталь закалена как надо, после определенного воздействии ( например, искривления ) она может возвращаться в свою исходную форму.
5160 пружинная сталь
В ней содержится 7% хрома — не достаточно, чтобы получить нержавеющую сталь (где нужно минимум 13%). Выкованный из такой стали, получается очень прочным.
5160 сталь так-же использовалась знаменитым Nepalese Khurki. Он создал невероятно острый и прочный меч, с помощью которого одним ударом отрубили голову буйволу.
Опять же, все зависит от закалки. Плохо закаленный меч из стали отличного качества может оказаться бесполезным.
9260 сталь
VIDEO: Flex Test
На видео меч возвращается в исходную форму, будучи изогнутым на 90 градусов!
Мечи из 9260 стали почти в два раза прочнее мечей из 5160 стали ( как пишет efunda.com )
Тем не менее такие мечи так-же могут ломаться.
VIDEO: 9260 Sword Breaking
На видео показано, как меч ломается при плохом ударе о толстую кость (толще, чем любая человеческая кость).
Мораль — любой меч может сломаться…
Инструментальная сталь
В последнее время эта сталь достаточно популярна — из нее получаются прочные острые мечи. На рынке существуют несколько типов данной стали. Мы поговорим о двух из них : T10 и L6 Bainite
Инструментальная сталь T10
В этой стали из вольфрамового сплава содержится высокий процент углерода (1%). Обычно это сталь называют «высокоскоростной».
T10 — очень твердая сталь (HRC60), и мечи, правильно закаленные, очень прочны. Благодаря вольфраму мечи из Т10 устойчивее к царапинам, чем другие мечи с таким-же содержанием углерода. Они так-же сравнительно тяжелее.
VIDEO: Destructive Testing of a T10 Tool Steel Sword
На видео показано, что мечи из Т10 очень прочны.
L6 BAINITE
Это так-же инструментальная сталь, ( используется для изготавления пил для разрезания гипсовой повязки ) где L — низколегированный сплав.
Когда закалены как следует, такие мечи считаются самыми крепкими. Такая репутация появилась у мечей из L6 благодаря работе Howard Clark из Bugei Trading company, который в поздних 90х производил мечи ручной работы из L6.
Такой меч трудно закалить ( из-за жесткости стали ), и так-же нужно постоянно поддерживать в хорошем состоянии, не давая ему заржаветь. Мечи из L6 — самые дорогие ( от 1000$ США)
Дамаская сталь
Катана из дамаской стали
у многих людей возникает вопрос о дамаской стали, и многие считают её лучшей для мечей.
Но даже зная это, у многих людей создается впечатление, что такая сталь прочнее других, и лезвия мечей, сделанные из такой стали, острее.
Это не правда.
Что касается японских мечей, — исторически такая технология применялась к японской железной руде (не очень хорошего качества) чтобы улучшить ее свойства. С качеством руды на сегодняшний день такие меры не обязательны.
swordmaster.ru